How Viscosity Impacts Tubing Choice in Peristaltic Pumps
- July 22, 2025
- ENQUIRE NOW
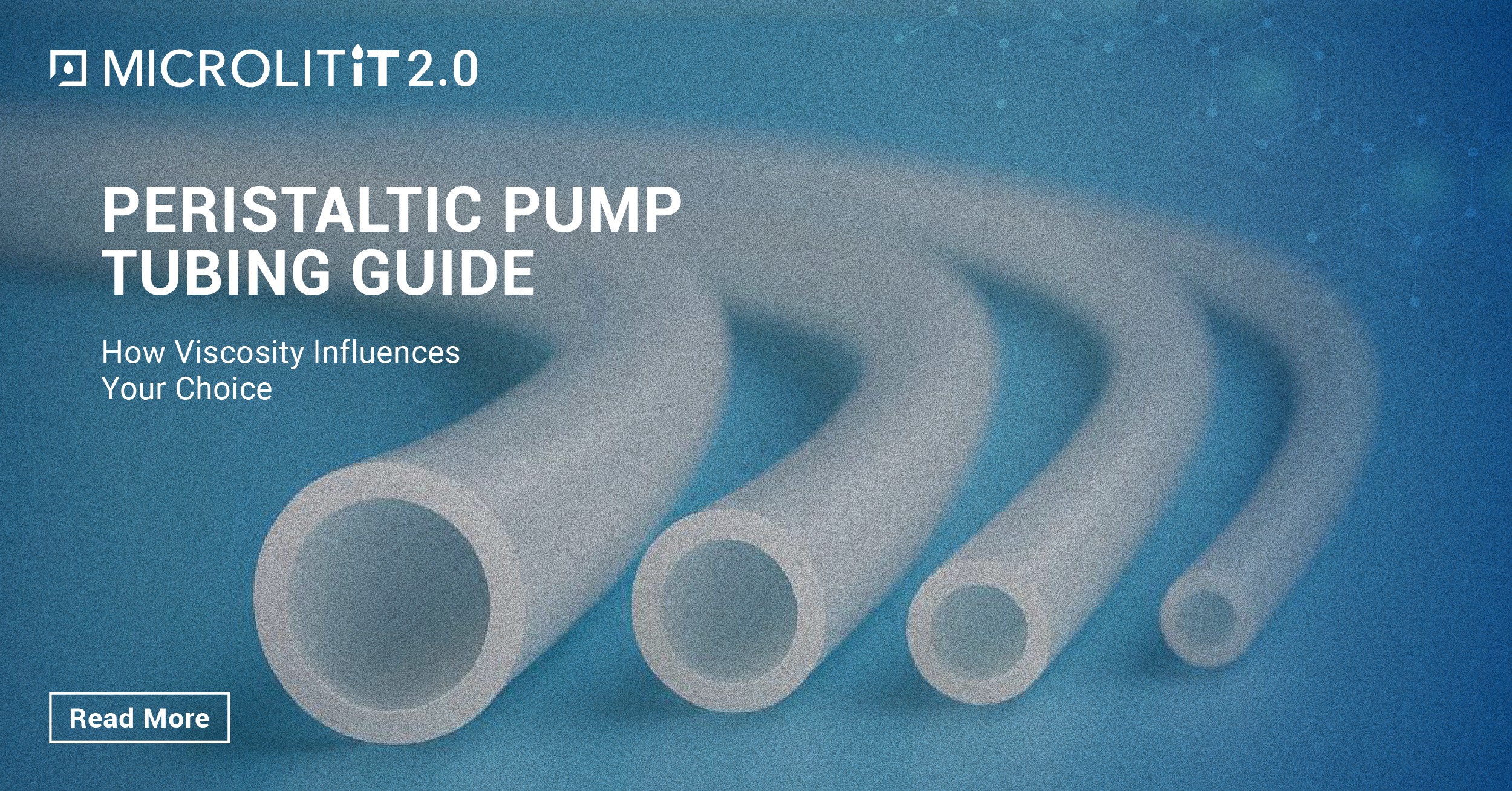
When selecting tubing for a peristaltic pump, one of the most critical—yet often overlooked—factors is the viscosity of the fluid being pumped. Whether you’re handling water-like liquids or thick, honey-like substances, viscosity directly impacts flow rate, tubing wear, system pressure, and pump performance. Choosing the wrong tubing can result in under-delivery, tube failure or inefficient processing.
Let’s understand why viscosity matters and how to match it with the right tubing specifications: type, internal diameter (ID), outer diameter (OD), wall thickness and channel configuration—to help you choose the best tubing for high-viscosity pumping applications.
What Is Viscosity?
Viscosity is a measure of a fluid’s resistance to flow. Low-viscosity fluids (like water or alcohol) flow easily, while high-viscosity fluids (like glycerin or molasses) resist movement and require more force to pump.
There are two types of viscous fluids such as,
- Low-Viscosity Fluids like water, or ethanol as they can pass freely from tube of pipes.
- High-Viscosity fluids like glycerin, molasses, or gel, these arw thick in texture so will restrict their movement. Further, need more pressure to pass through tubes.
Everyday Viscosity Examples:
Water: ~1 cP
Olive Oil: ~80 cP
Honey: ~10000 cP
Glycerin: ~1200 cP
A fluid’s viscosity is not always constant, depending on the temperature, so it’s important to account for the operating environment when setting things up.
How Does Viscosity Impact Flow Rate?
Flow rate in a peristaltic pump system is not constant, it changes according to:
- Tubing internal diameter (ID)
- Pump speed (RPM)
- System pressure
- Viscosity of the fluid
General Formula of Flow Rate
Flow rate (ml/min) = RPM × Flow per revolution × Viscosity correction factor
As viscosity increases, the flow rate decreases, often by 20% to 50% compared to water. Therefore, it’s advisable to perform test runs or calibrate the pump with your actual fluid before full deployment.
Microlit Tip: Use a real-time flow sensor to monitor changes when working with temperature-sensitive or viscous substances.
Why Viscosity Matters in Tubing Selection?
1. Tube Material Compatibility
Viscous liquids cause more drag and put more stress on tubing. Silicone vs Viton tubing can respond differently under pressure, for instance.
- Silicone works well for thin aqueous fluids but can deform on heavy fluids.
- PharMed BPT and Norprene provide additional mechanical strength for heavy-duty or viscous service.
- Viton resists heat and is the choice for oils and solvents.
Microlit Tip: Always equate your fluid’s chemical and mechanical properties with a tubing material made for durability.
2. Tubing ID and OD Selection
Selecting the appropriate tubing ID and OD (internal and outer diameter) is most critical to keeping flow rate.
- For low-viscosity fluids, a smaller ID (e.g., 1.6 mm) provides accuracy.
- For high-viscosity fluids, a larger ID (e.g., 4.8 mm) is necessary to cut down on back pressure.
Note: Wider IDs enhance flow but can decrease pressure and precision. Always balance flow demands with system stability.
3. Wall Thickness and Strength
Heavy-duty wall tubing (at least 1.6 mm) is necessary for withstanding collapse, particularly under high RPMs or when pumping fluids over 1000 cP.
Heavier walls also enhance occlusion, the tubing-pump roller seal—vital for pulsation-sensitive applications in biotech, pharma, or food dosing.
Microlit Tip: For viscosities over 600 RPM or over 1000 cP, use tubing with a minimum wall thickness of 1.6 mm.
4. Number of Channels & Pump Head Selection
Multi-channel pumping head with viscous fluid necessitates even distribution. The thicker the fluid, the greater the chances of uneven channel flow.
For this, utilize a pump head for viscous fluids such as the PH15T or PH25, which is designed to deliver pressure and occlusion. Also, restrict active channels when dealing with fluids over 5,000 cP.
How to choose Tubing based on Viscosity?
The correct tubing type is determined by viscosity and fluid compatibility:
- Silicone: Excellent for water-based solutions; restricted to ~8000 cP.
- PharMed® BPT: Exceptional for biological and viscous fluids (~10,000 cP).
- Norprene®: Best for industrial fluids and for long-term use.
- Viton®: The best for chemical resistance and heat endurance.
- PTFE/FEP: Best suited for highly corrosive or heavy-duty liquids; not as flexible.
Practical Use Cases
Here’s how various industries deal with their high-viscosity pump setup installation:
Pharmaceutical gels (approx. 10,000 cP): Utilize PharMed® BPT tubing of 3.2 mm ID and 1.6 mm wall thickness.
Industrial lubricants (approx. 3,000 cP): Norprene® with reinforced walls is the best choice for reliability.
Honey in food processing: Viton® or Tygon® are utilized for their thermal and chemical resistance.
Conclusion
Viscosity is not a number; it’s a determining factor in your high-viscosity pump system. From tubing material through ID, OD, wall thickness, and pump head design, each point must cooperate with your fluid’s flow characteristics.
There are various benefits of carefully selecting a peristaltic pump tubing, this can make the flow of an experiment smooth. Further enhancing the tubing life, lower maintenance and improved accuracy. While choosing, check your fluids viscosity and select tubing scientifically, this will eliminate the chances of wear and tear of the tube.
If you are still confused and looking around the different shapes and sizes of a tube, without making a fuss, connect with us at Microlit. We will guide you through the knicks and knacks of the tube choices and we are experts in providing cost-effective and dependable solutions for your lab-quality liquids, industrial lubricants or food-grade gels.
Contact Microlit today at info@microlit.com and enjoy precision for every drop.