How to remove air bubbles from any liquid handling instrument?
- May 23, 2022
- ENQUIRE NOW
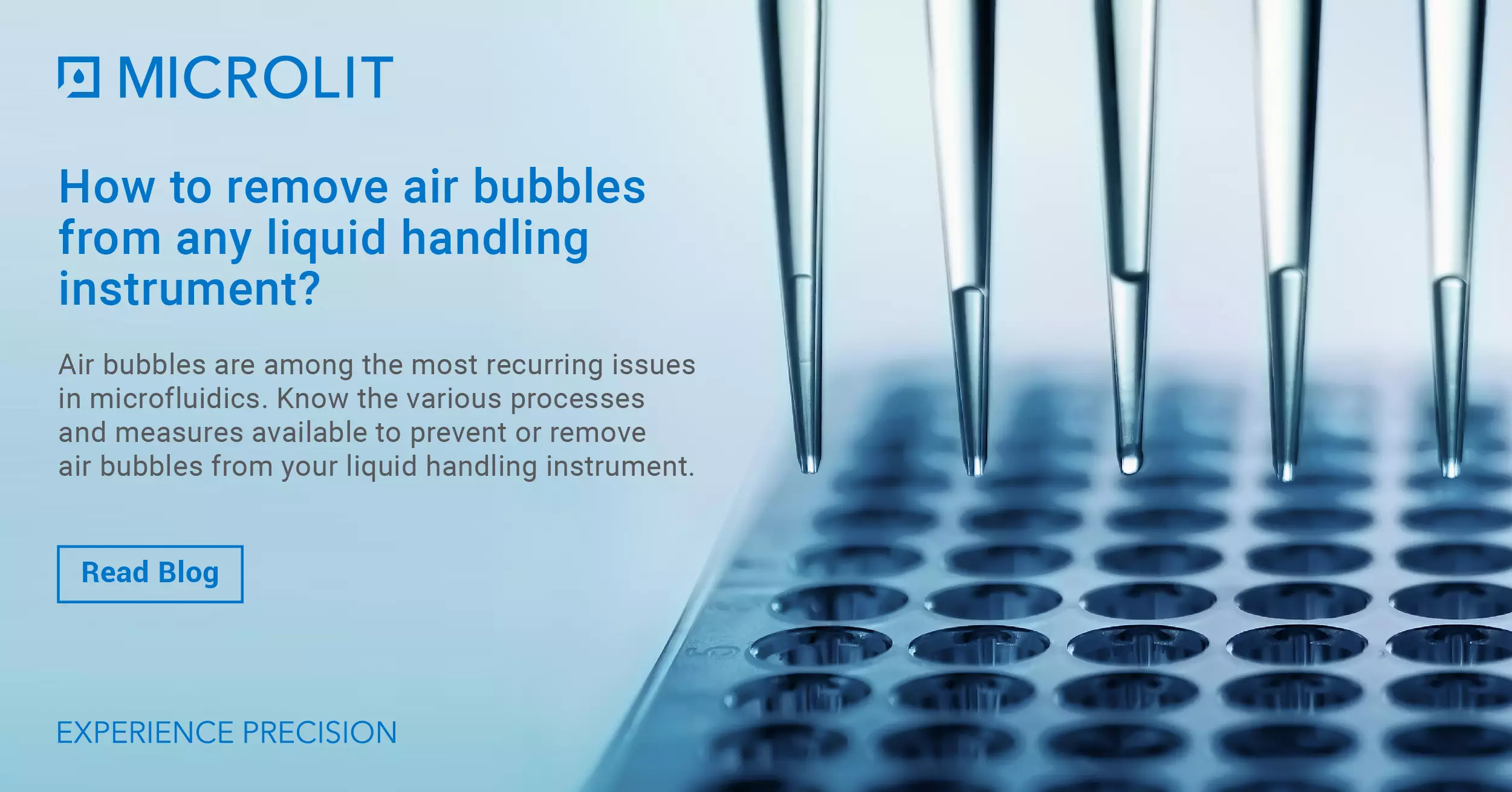
Introduction to air bubbles in liquid handling devices
Air bubbles are among the most recurring issues in liquid handling instruments. Various types of liquid handling instruments include a variety of automated robotic systems like digital/electronic pipette, micropipette with fixed or disposable tips, microplate/microtiter plate, dispensers, stackers, handlers, washers, etc and because of the micrometric dimensions of the tubes and channels of these devices, air bubbles can be very difficult to remove and be detrimental to the experiment being conducted. Removing air bubbles will eliminate false readings and other dispensing anomalies and simultaneously improve the volume precision and dispensing accuracy of the instrument.
The origin of air bubbles inside liquid handling devices
In a solution, air bubbles are formed when the dissolved air amount surpasses the saturated solubility. The state in which the amount of air dissolved in a solution upon exposure and the amount of air entering and leaving the solution remain in equilibrium is known as the saturated solubility. The saturated solubility may vary depending on the type of solution, gas, temperature and pressure.
In liquid handling devices, the first step of eliminating air bubbles is the identification of their points of origin as discussed below:
Experiment start: Following the initiation of an experiment, a large or required volume of liquid is circulated, filled, moved or transferred in the devices. This point is critical, as the movement of liquid in a setup can cause air bubble entrapment or residual bubbles.
Liquid transfer: During the experiment, the transfer of liquids from one container to another cause air bubble entrapment. This could be due to fluid viscosity, pressure and flow rate.
Excess liquid: Considering the dimensions, sheer size and capacity of the device, the excess volume of liquid can itself trigger air bubbles.
Leaking: Air bubbles can appear during the experiment if one or several fittings are leaking in a liquid handling setup.
Dissolved gas: The gas entrapped in liquid can also cause air bubbles formation, especially when the liquids are heated as the saturated solubility of gases gradually decreases with an increase in temperature resulting in excess dissolved gas forming bubbles.
Issues created by air bubbles inside liquid handling devices
The air bubbles issues are not only detrimental to the equipment, but also to the experiment being performed as well. Both of these issues are discussed below:
Equipment issues
Flow instability: The air bubbles’ presence directly affects the liquid flow due to a velocity difference between the liquid and the gas. The other contributing factors are suction, discharge and piping configuration.
Flow rate: The trapped air bubbles in a device may cause an increase in the time needed to reach a pressure equilibrium, thus affecting the flow rate.
Resistance: The air bubbles in any device will naturally pose a resistance directly influencing liquid pressure and flow.
Experiment issues 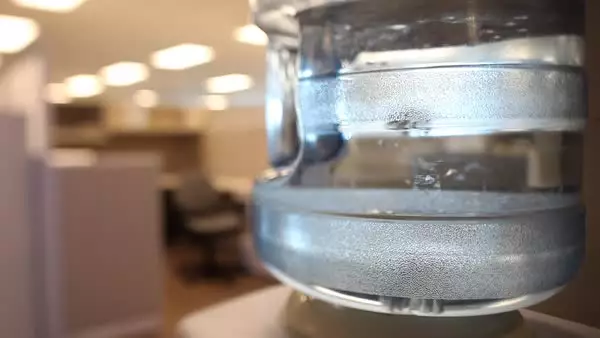
Interfacial tension: Air bubbles cause an interfacial tension in a liquid. This could damage the experiment entities such as cell culture by applying unnecessary stress on cells, leading to cellular death.
Aggregation: The interfaces between the air bubbles and the liquid may accommodate particles or protein aggregation. They serve as artefacts and may result in failed experiments.
Configuration: The recurrent air bubbles may pose shear stress and pressure on the device walls, damaging the equipment’s configuration and grafting.
Calibration: The calibration of the equipment could also be affected by the presence of air bubbles, as increased airspace results in a smaller/altered volume of liquid.
Issues created by air bubbles inside microfluidic devices
Flow modifications
Flow instability: The presence of air bubbles, moving in the fluidic setup, or dilating/contracting, can cause an important flow rate instability.
Compliance increase: When an air bubble is trapped somewhere in your fluidic setup, the time needed to reach pressure equilibration can increase. Indeed, when applying a pressure change, the air bubble will absorb some of the pressure switches by dilating or contracting. This effect can be particularly detrimental when a good fluidic reactivity is needed.
Resistivity increase: When one is trapped inside a microfluidic channel, it will act as an additional fluidic resistance by reducing the diameter of the channels. This can cause important issues, especially when working with syringe pumps which apply a fixed flow rate. The pressure inside the microfluidic chip will then increase significantly.
The interactions between the air bubbles and the experiment can be detrimental in many ways. Some of the most common ones.
Interactions with the experiment
Cell culture damage: Air bubbles present interfacial tension that can apply stress on cells and even lead to cellular death.
Aggregation at interfaces: The interfaces between the air bubbles and the liquid are an area where potentially, particles or proteins can aggregate, leading to artifacts in the experiments.
Wall functionalization damaging: When passing through the microfluidic channels, they can damage the chemical grafting previously made.
How to remove bubbles in liquid handling devices?
There are various processes and measures available to prevent or remove air bubbles. Although not universal, these processes can do a great service to the equipment and experiment as well. They are categorised below:
Preventive measures
Fittings: The loose-fitting may serve as a possible entrance for air bubbles. The adhesives or Teflon tape can be used to obtain a leak-free setup.
Liquid degassing: The degassing of liquids before the experiment, if possible, can help reduce bubbles formation, especially when the liquids are required to be heated during the experiment. The saturated solubility of gases gradually decreases as the temperature increases resulting in air bubbles.
Injection loop: Using an injection loop can help you overcome the issue of bubbles entering the system when adding a new liquid. When using an injection loop, a capillary is filled with the sample you want to inject and some liquid (such as a buffer) pushes the sample.
Corrective measures
Pressure pulses: The maintenance of pressure could be a preventive measure as well. If the gas at saturated solubility is at high pressure, air bubbles will form when the pressure is decreased. Applying pressure pulses and controllers is a good way to detach air bubbles. However, this measure could be troublesome for a fragile device.
Bubbles dissolution: Alternatively, air bubbles that are hard to detach can be dissolved by applying pressure or introducing a soft bioinert surfactant. A buffer solution with surfactant can be flushed through a liquid handling set-up to facilitate the reduction of surface tension at the liquid-gas interface by adsorption.
Soft surfactant: In order to help detaching the bubble, a buffer with a soft surfactant (such as SBS) can be flushed through the fluidic path.
Debubbler: They are a microfabricated tool, introduced in a liquid handling assembly, to remove visible air bubbles from a fluid stream without the aid of surfactants. When coupled with vacuum degassing, the debubbler eliminates existing bubbles as well as dissolved gases. For example, Biotech’s patented debubbler is designed with a vertical bubble trap, gas-permeable membrane and a vacuum source for combinatorial effect.
Microlit Beatus and Lentus™ is a Bottle Top Dispenser (BTD) that works on Recirculation Valve technology. Recirculation Valve prevents the loss of reagents during purging by re-directing them into the mounted bottle and facilitates bubble-free dispensing. It helps in achieving precision with reliability in practical laboratory environments.
Microlit is a leading name in Healthcare and Life Sciences that provides liquid handling instruments with higher precision and analytical accuracy in compliance with ISO standards. Our products are developed keeping in mind the durability with easy maintenance and use for their consumers, providing them with a robust, innovative and efficient experience. Our product range includes Bottle Top Dispensers, Electronic Burettes, Micropipettes, Miniature Micropipettes and Electronic Pipette Filling Instruments. Other instruments like Micropipettes Stands, Tips and Tip boxes are also available. For any query/demo/installation, feel free to email us at info@microlit.com